Bringing Circuits to Life: Techniques in PCB Assemblage
Printed outlet boards (PCBs) are really the workhorses of modern electronics. These intricate boards hold various electronic parts like resistors, capacitors, and integrated circuits (ICs), ensuring their own connection and operation. PCBs come in various complexities, ranging from single-layered regarding simpler devices in order to multi-layered for superior electronics. They're usually made from protecting materials like fiber glass and bonded using copper to make conductive pathways.
Typically the Crucial Stage: PCB Assembly
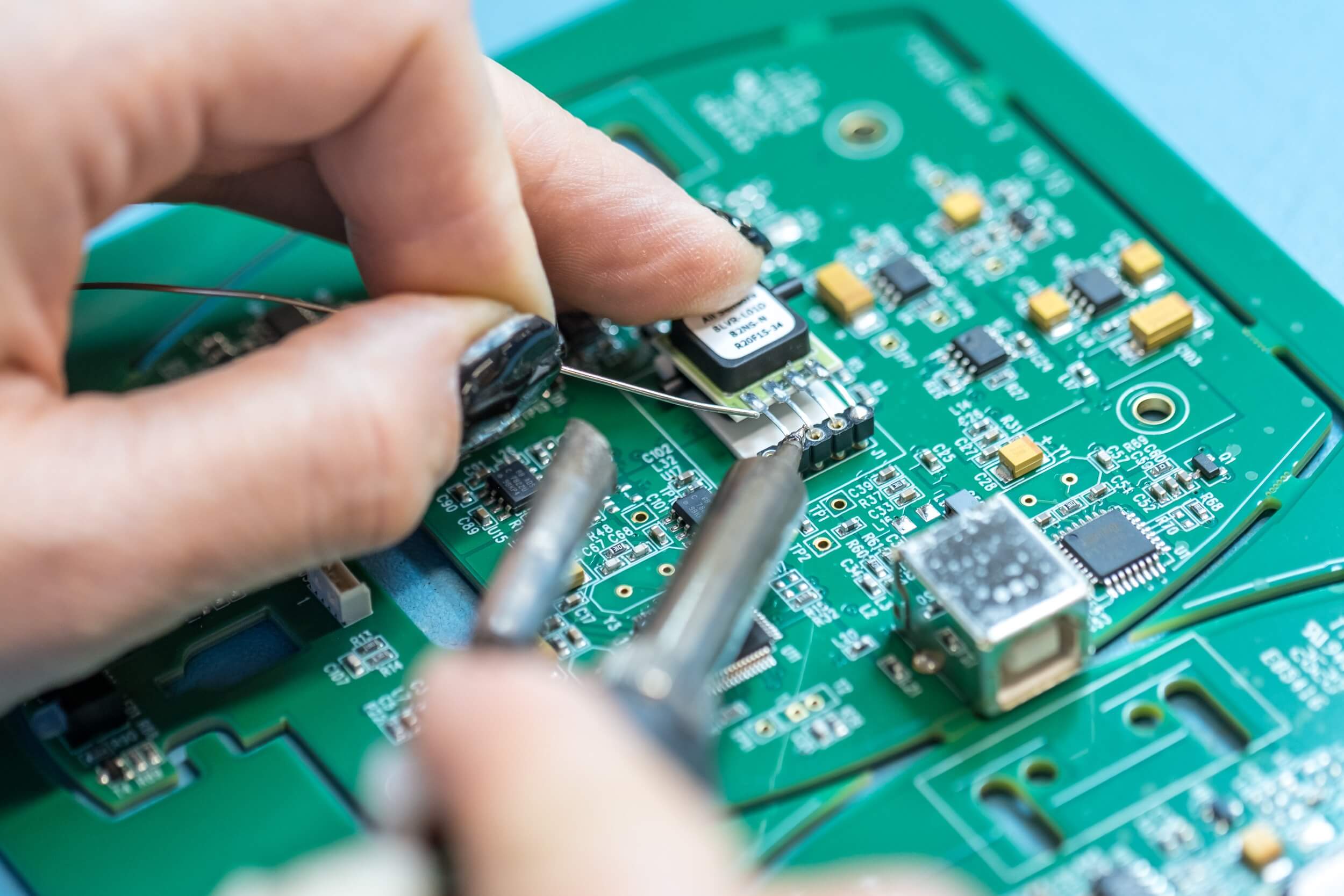
PCB set up is an important step after PCB fabrication. Here's in which the magic happens: electric components are placed on the board to create a functioning circuit. electronic manufacturing Reno Nevada of assembly technique will depend on several factors, like the type of PCB, component size, in addition to circuit complexity.
Through-Hole Technology (THT):
Traditional and Robust: Through-hole technology (THT) is definitely a well-established method, commonly used regarding single-layered PCBs.
The task: Holes are drilled into the PCB to allow the aspect leads (pins). These leads are after that inserted through the particular holes and soldered onto the contrary side of the board, firmly securing the constituents. Adhesives may also be used for additional strength.
Advantages: THT offers strong physical connections, making this suitable for applications requiring durability, such as industrial equipment or devices susceptible to shocks. Larger components using thicker leads are also well-suited for THT.
Surface-Mount Technological innovation (SMT):
Modern Miniaturization: Surface-mount technology (SMT) is a dominating technique for complex, multi-layered PCBs used inside of modern electronics.
The Process: Components using flat leads or terminals are soldered directly onto the particular PCB surface utilizing a solder paste and even reflow soldering procedure. This allows regarding a higher denseness of components, leading to smaller and even more compact devices.
Positive aspects: SMT enables miniaturization, making it ideal for space-constrained equipment like smartphones plus laptops. It also features faster assembly plus potentially lower costs as a consequence to automation.